Photographs taken 2010
The Tin Mill is an excellent place to learn more about tin processing, and the guides that work here now, not only are very knowledgeable about their subject, but many actually worked here when it was a working processing mill, and the whole experience of a visit to Geevor Mine can only be thoroughly recommended - see the Geevor Mine Website.
The preserved Tin Mill at Geevor is attached to the Victory Shaft, and processed ore (Cassiterite) was brought to the surface through this shaft, and transferred directly from the kibbles to the mill via conveyor belts. The modern building and tin mill that stands on this site date from as late as 1980, before its final closure in 1990 and the road to conservation, but some parts of the mill date back to the 19th century and the days where tin processing techniques were very different. Tin processing itself is also known as "tin dressing", and was carried out on the "dressing floors". These were where the bal (mine) maidens used to work while their men mined the ore underground. Techniques then would have involved a lot of hand, and hard, labour to break the rocks by hand before the mined ore could be further refined. This would have included "ragging" (with sledgehammers), then "spalling" and "cobbing" with smaller hammers as the pieces were broken smaller and some of the waste was removed. The cobbed ore was then sent to the "stamps" - powerful water-wheel driven (or later steam-driven) lifting stamping hammers that crushed the ore to "pulp" the watery wash of crushed rock and ore that was sent for refining in the buddles. The buddles were effectively gravitational separators to separate out the heavier tin ore from the waste, and these techniques were further improved over the years into the twentieth century using tables. All these processes were carried out - usually in the open - on what were known as the dressing floors, which covered a large proportion of the surface workings of a nineteenth century tin mine.
Tin processing and dressing at Geevor, with the new tin mill, took place under cover, and the equipment installed was more advanced, though it essentially did the same thing - to derive the "black tin" - the refined cassiterite ore ready for sending for smelting. The image below shows the top of the Tin Mill to the left of the Victory Shaft, at the top of the slope down through the rest of the mill, where the broken rock first enters the mill to be crushed.
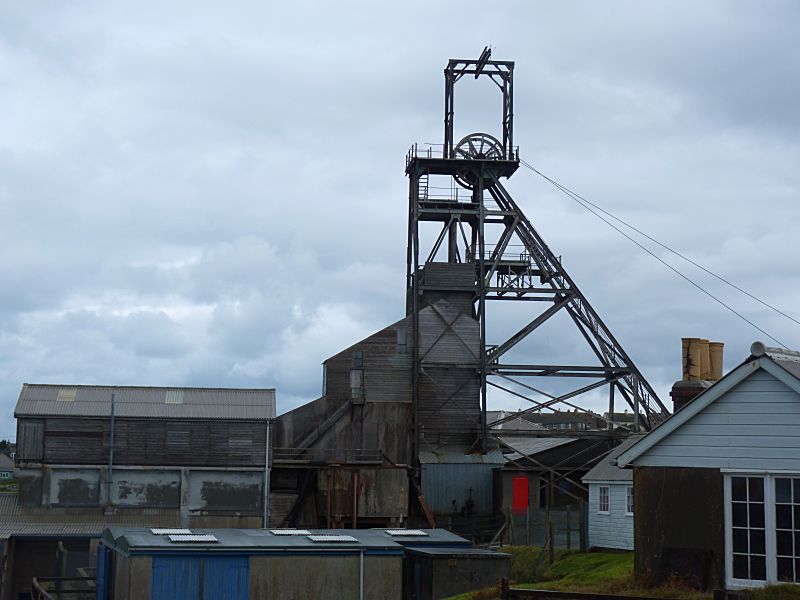
Geevor Mine and Victory Shaft - the top end of the preserved Tin
Mill is to the left
Before the ore entered the mill, it is useful to see where it came from in the first place... Geevor Mine was managed as were most mines, by the Mine Captain. His office is still preserved at Geevor as perhaps it might have been seen with the mine still being worked around it - though it is eerily quiet now. The board shows a stope where the ore was mined from the "lode" or the vein of ore in the bedrock, or the "country" rock as it was called.
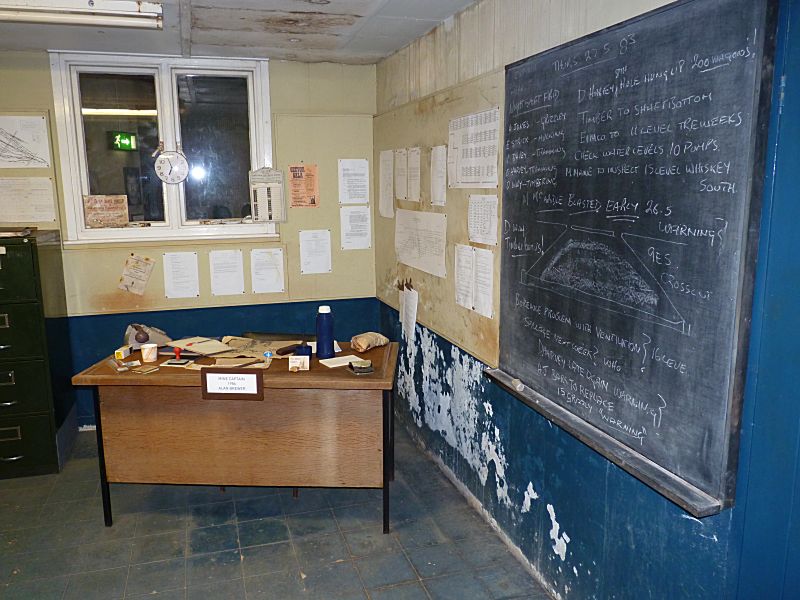
The Mine Captain's Office
One of the boards in the Geevor Museum shows schematically how
this ore was won from the stopes and various levels in the mine by
drilling and blasting, and then "trammed" along to the shaft for
lifting to the surface. Some limited breaking of the ore also took
place underground, while the ore was still in the stopes and
manually broken through heavy grids or iron girders - large
"grizzlies" - before being trammed out.
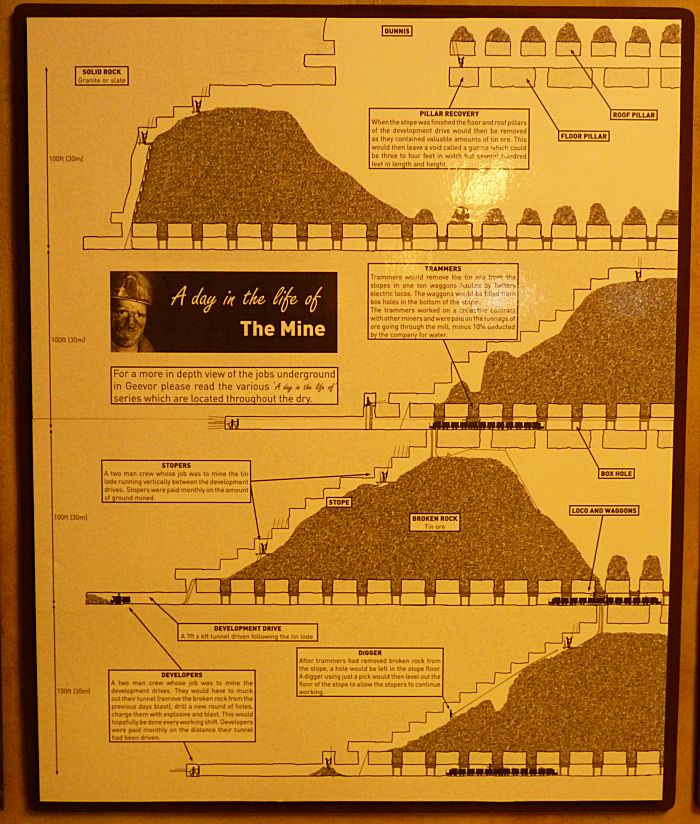
How the Tin Ore - Cassiterite - was mined by drilling and blasting
These two photos show a reconstruction of an "overhand" stope, where a miner is drilling prior to blasting...
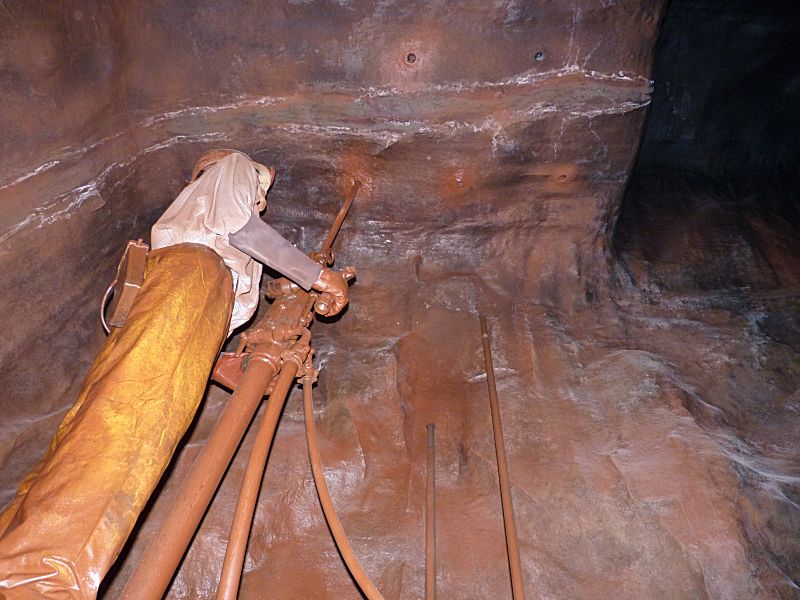
A mock-up in the Hard Rock Museum of how the ore was won from the
stopes
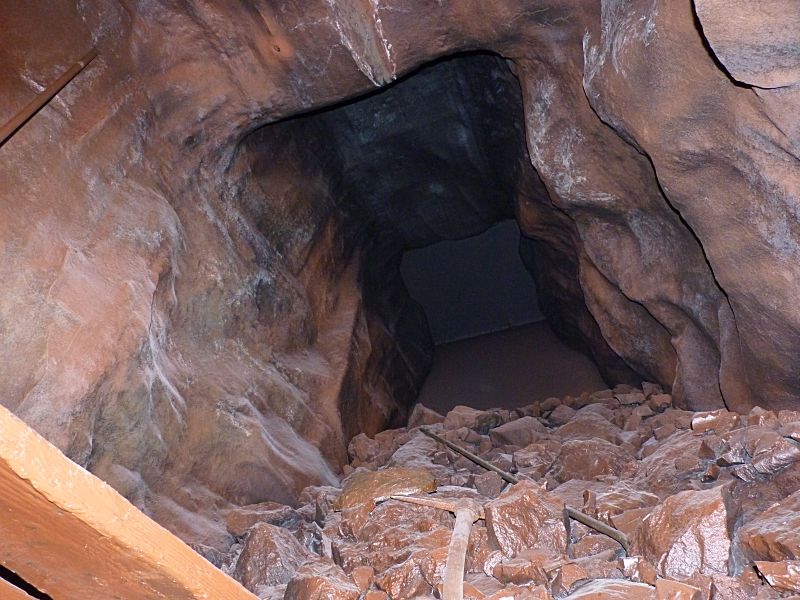
Looking up the mock-up stope with the blasted rock fallen down ready
for breaking and tramming out
Once brought up the shaft, the broken, mined ore was transferred to the mill, where one of the first tasks was to pick out the inevitable rubbish that was brought up in the kibbles - whether it be the odd glove(!) or iron contamination which from an old mine will appear from time to time. This was a manual inspection operation, but was helped by a large powerful electromagnet that could also pick out unwanted heavier ferrous material or iron ore based rocks that were present.
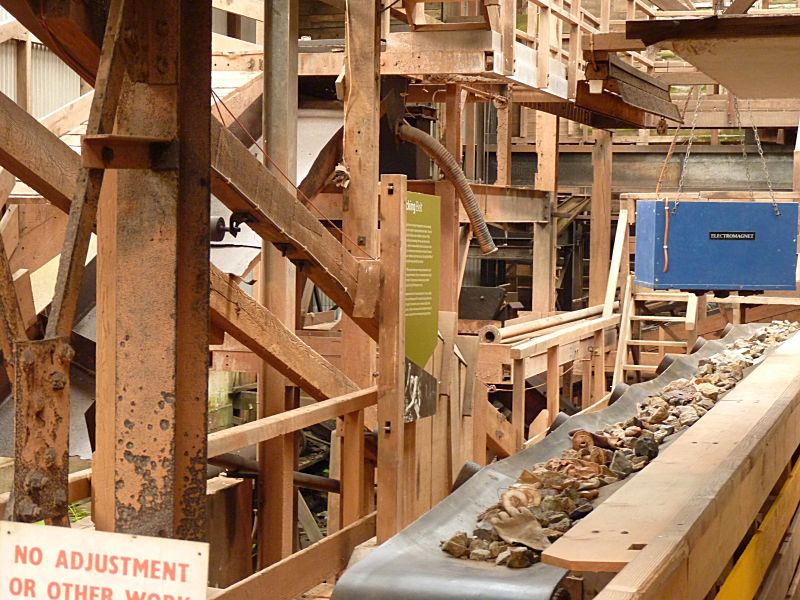
The "Picking" Belt
After the mine closure, some processing equipment including the more modern ore crushers that would have taken the place of the original more manual crushing processes, were sold off to presumably offset losses or to settle the company books. These crushers would have reduced the ore size down to the 10-20cm level for passing on to the grinders.
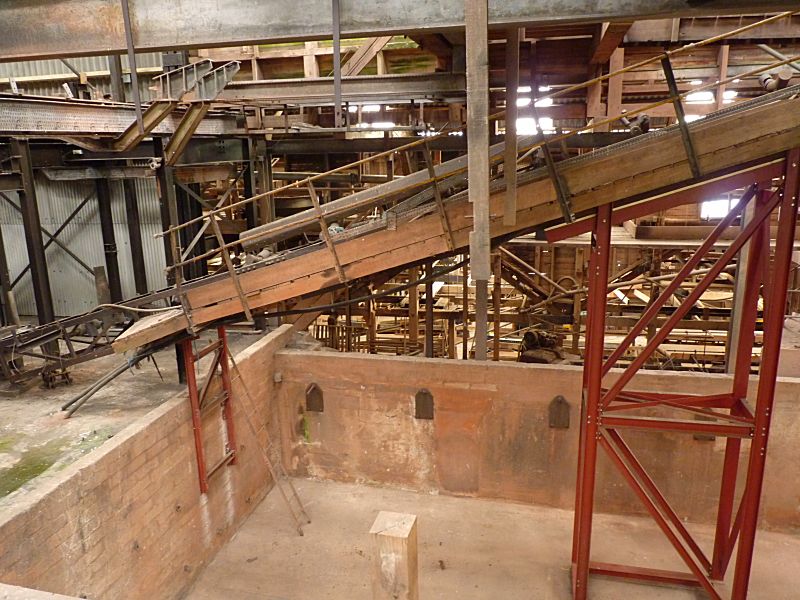
Past the now gone ore crushers...
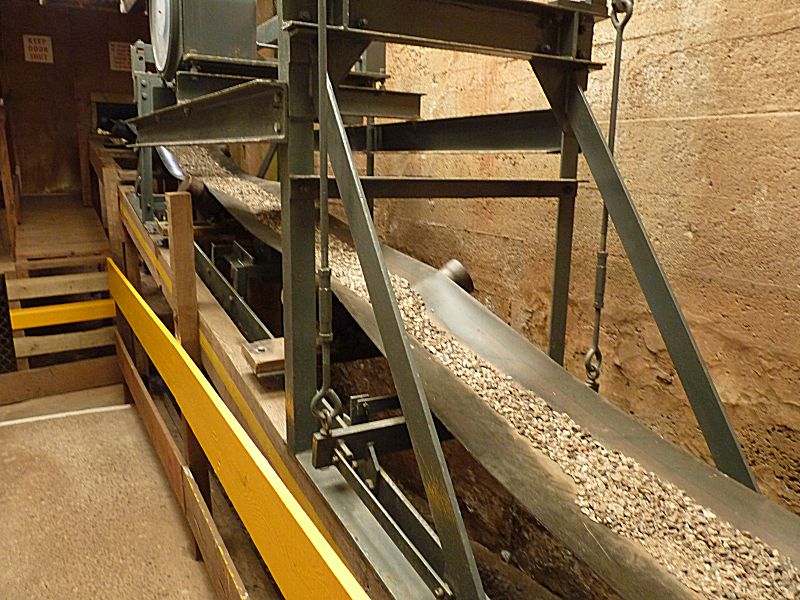
Ore crushed down to the 10 - 20cm size for passing to the ball
grinders
The grinding mill consisted of essentially large rotating ball grinding machines, that tumbled and ground down the ore much as a (highly!) glorified tumble drier might do! These grinders replaced the old steam-driven stamps that would have originally ground down the ore to the "pulp" watery-mix stage. The grinders shown below used heavy steel balls (like the ones on top of the grinder), and the ore was washed in with water until it was ground down to the size of sand, when it was discharged out - anything too large was cycled back in again. These ball mills replaced the stamps at Geevor in 1937.
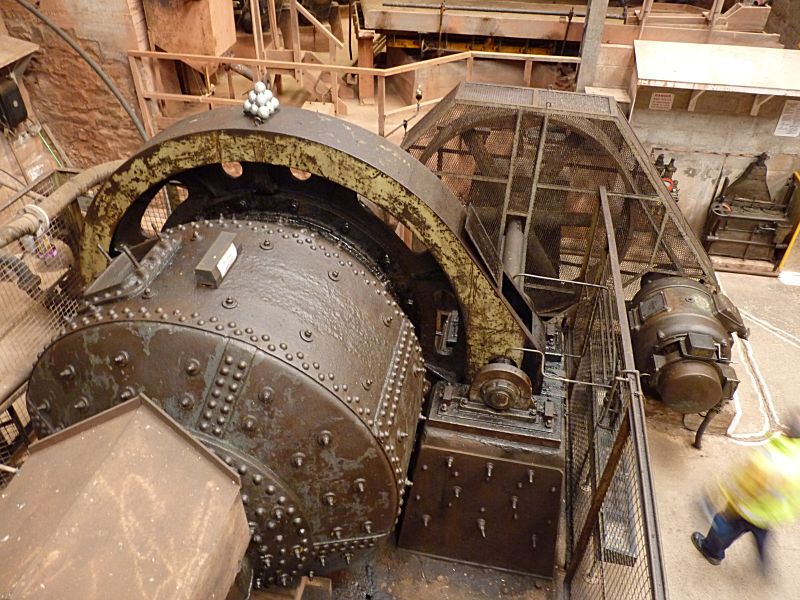
Ball Grinding Mill (and our guide ghosting in!)
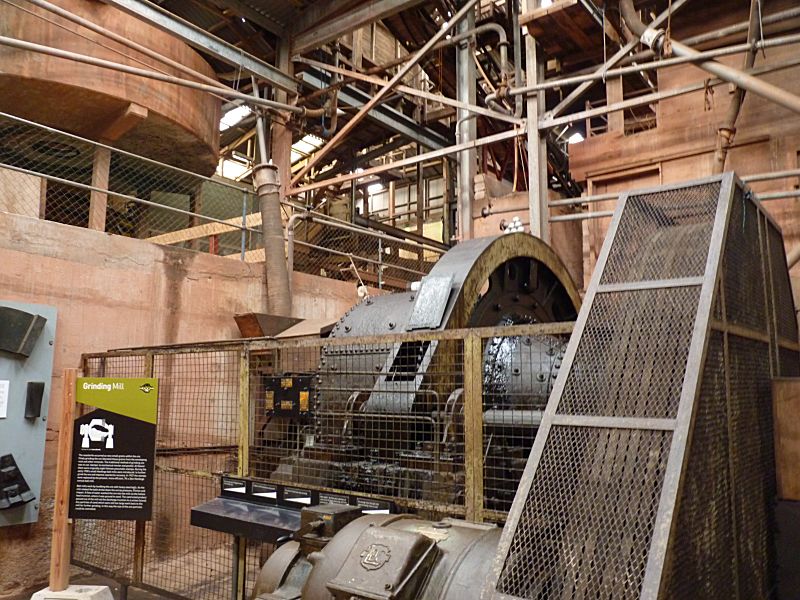
Another view of one of the Grinding Mills
With all this processing, only about 1% total of all the ore material entering the mill actually emerged as usable cassiterite grains for smelting as tin. The rest, excepting perhaps another 1%, was waste. To get the precious tin ore further reduced to the best quality material, a variety of refining techniques, or "classifying" were used. The most obvious and easiest to see working in the Geevor tin mill, were the Shaking Tables. These used the flow of water against gravity to settle out the heavier ore particles from the lighter waste product, which was washed out and away. The lighter waste was kept mobile in the water by the shaking, as the ore settled out against the shallow ridges on the table, and this refined ore material could then be taken off from the table surface when enough had accumulated. It could also be classified or "graded".
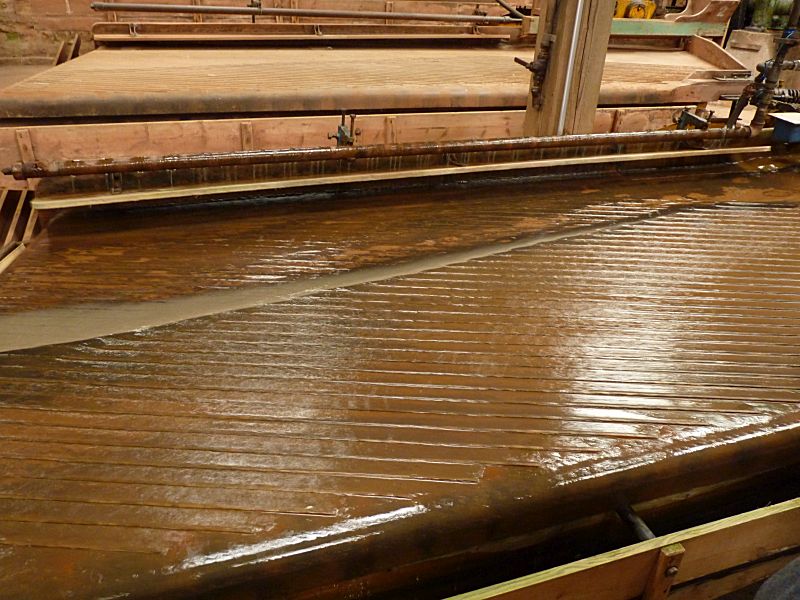
An ore Shaking Table in operation - the separated out ore is the
grey streak across from centre left
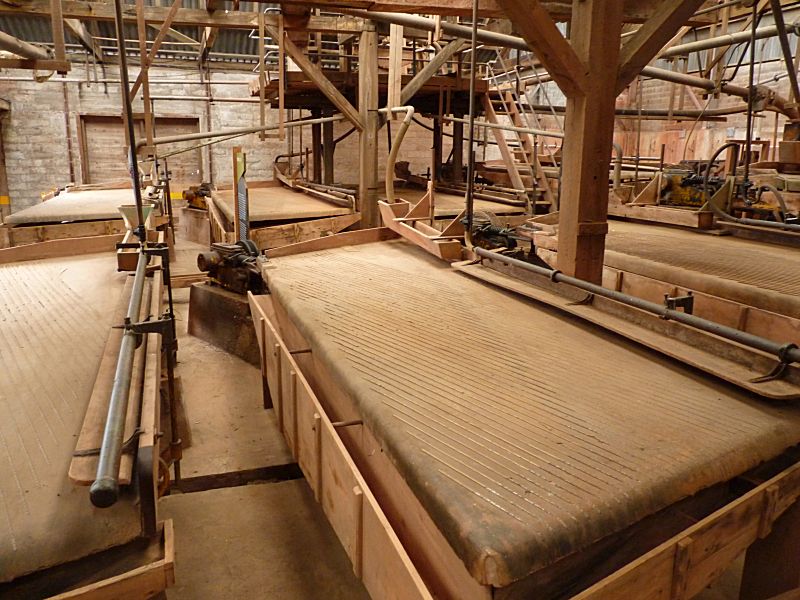
More Shaking Tables on the Dressing Floor
Some re-grinding was also carried out in the re-grinding mills shown below. These would presumably be used to further grind down some of the coarser material from the primary grinding and classifying processes.
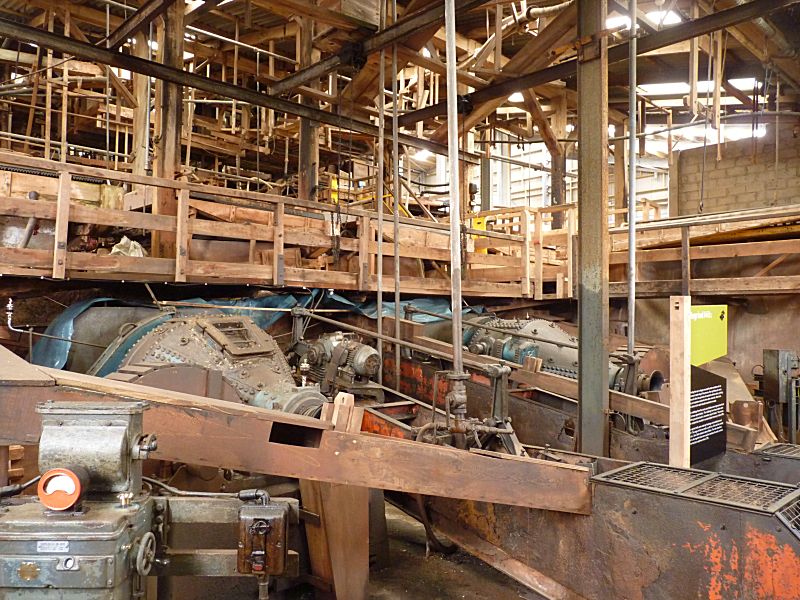
The Re-grind Mills below the Shaking Tables floor - not some strange
spacecraft!
Besides the grinding mills and shaking tables, other modern classifying methods were also employed at Geevor. These included "Froth Flotation". This replaced the original Calciner that would have been used to roast off the impurities such as Sulphur Di-oxide and Arsenious Oxide, to be deposited up a long flue and Labyrinth, such as the one at Botallack. This very unsavoury method - for the workers - was thankfully replaced when the Flotation process came into use. Flotation is a process by which the unwanted minerals are separated using chemicals to alter the surface of the mineral grains, to make them effectively repel water, thus "frothing" them off the surface. The heavy cassiterite would then be harvested from the bottom, and other minerals, even copper and gold could also be separated out using this technique.
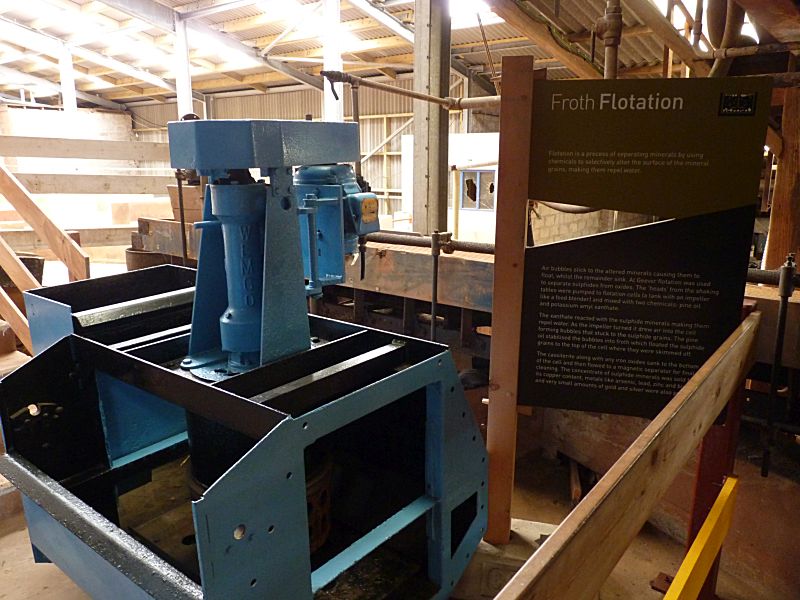
The Froth Flotation process - replacing the old Calciners
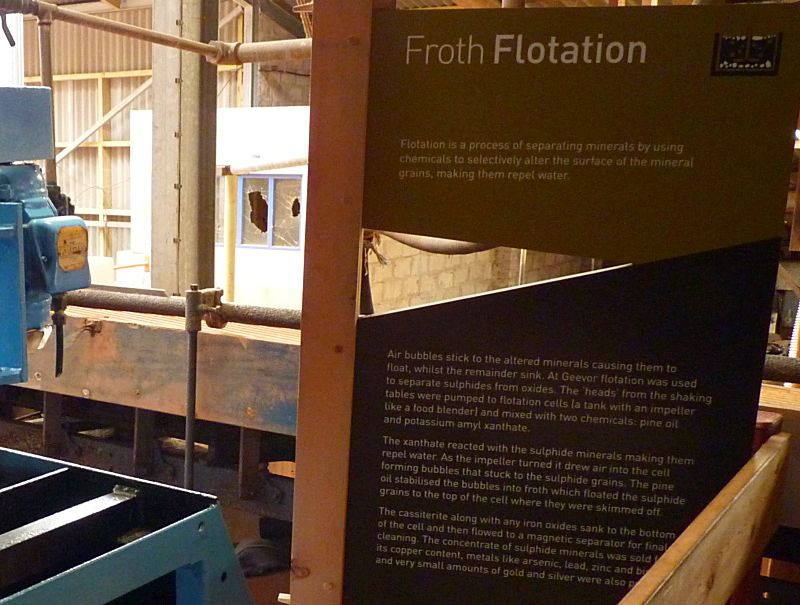
A close-up of the Froth Flotation description at Geevor
Another process was Magnetic Separation. This involved separating the adventitious iron minerals that were found in the refined ore material - either originating from the original ore, or from being picked up during processing, for instance the balls in the grinding mills. As tin is non magnetic (non-ferrous), the iron can be separated out by electromagnets. The resulting high grade cassiterite - the sought after "black tin" - could then be shipped out for smelting, knowing that it was free of impurities, and that it would yield as much as 72% tin (see the description board below).
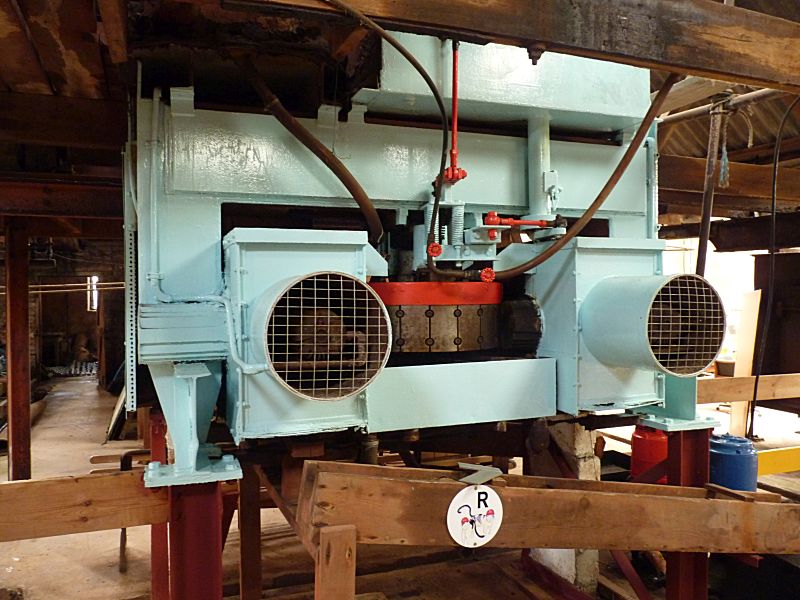
The High Intensity Magnetic Separator
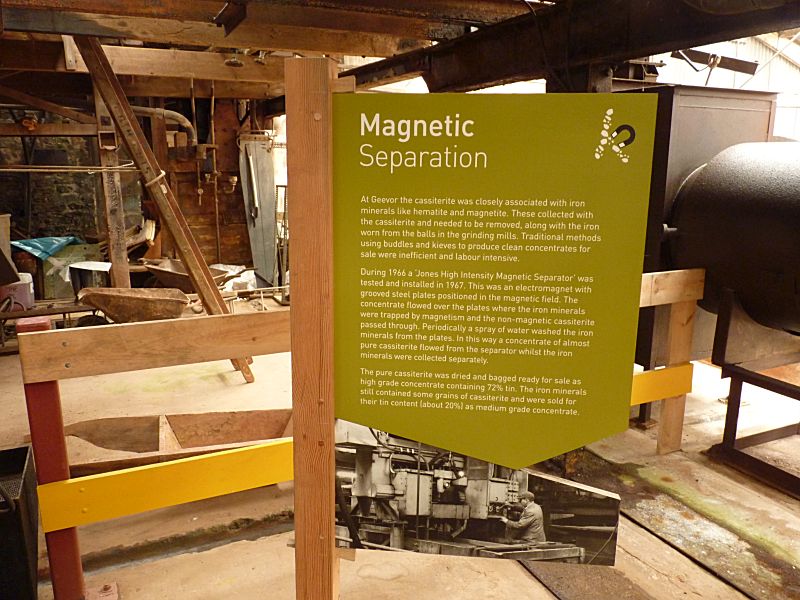
The Magnetic Separation process
The Miners' Dry - All Quiet Now
The Miners' Dry is essentially the miners' changing room. It was originally called the "Dry" back in the nineteenth century, when a room or a space near the main boiler for the beam engines was used for miners to hang their wet working clothes to dry over steam pipes, after their shift down the mine, ready for next time. This evolved into more modern changing and shower rooms, and personal lockers, that still retained the name "The Dry". It is this part of Geevor Mine that is the most poignant and moving monument to the miners who worked here, and to this end, their are photographs stand sentinel over all the walls. Their locker room stands as it was left on the last day in 1990, just as if they might return the next day.
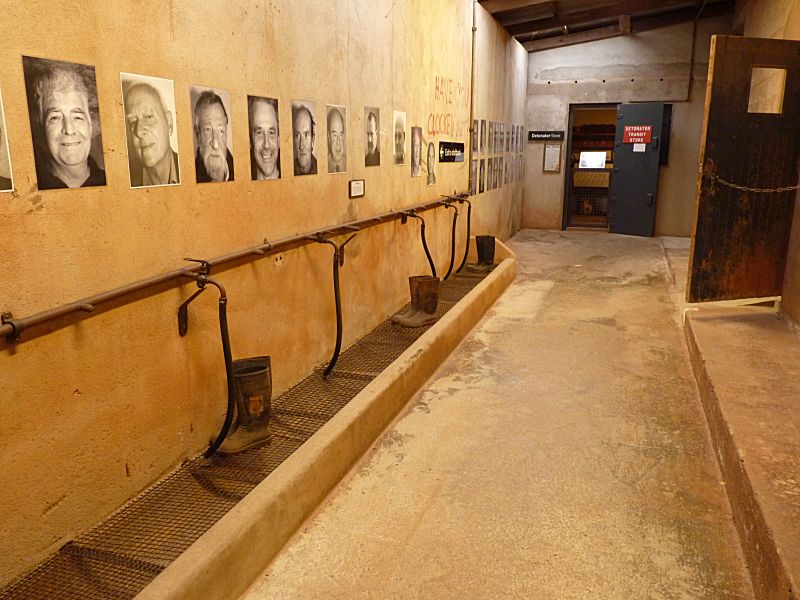
Boot cleaning coming off shift, and the miners who worked at Geevor
all round the walls of the Dry
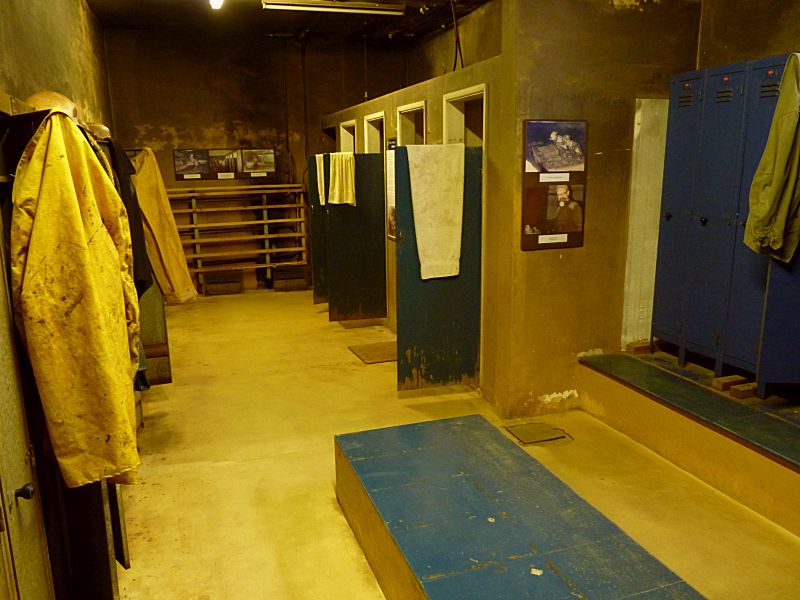
Lockers and changing areas
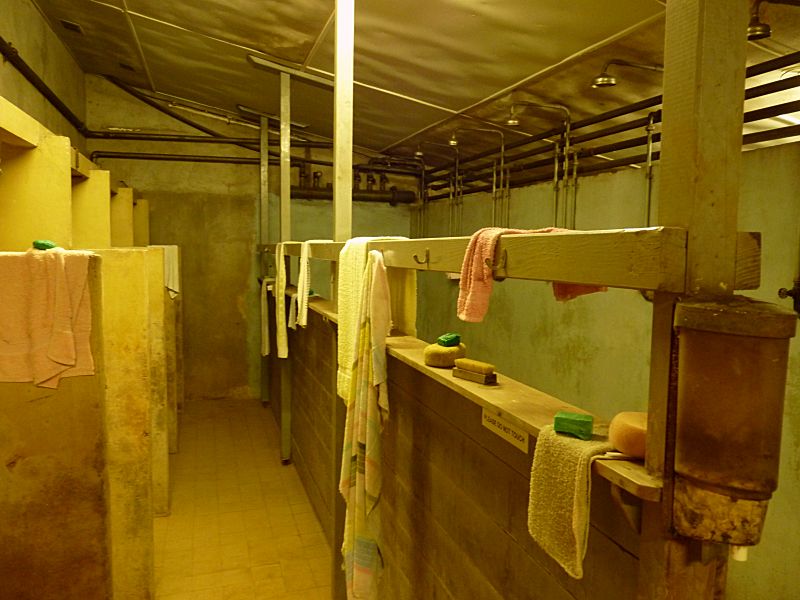
Some of the showers
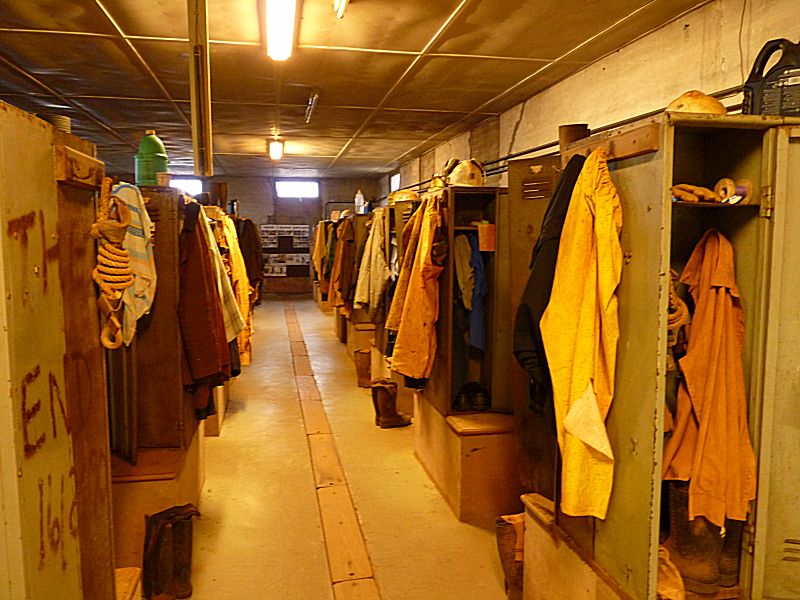
Abandoned Lockers as they were left on the last day of 16 February
1990 - and the final message on the left
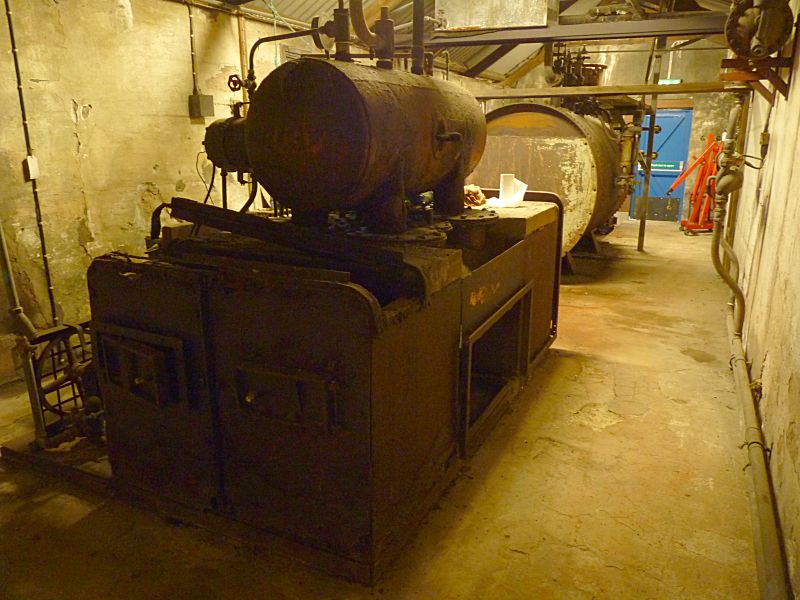
The now disused Miners' Dry Boiler House
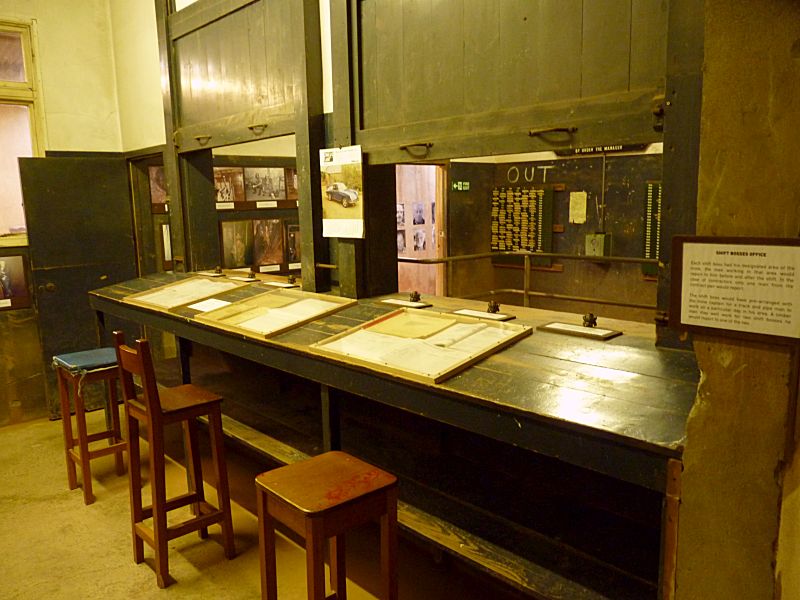
No more will Geevor Miners sign on and off in the Shift Office
See also Geevor Mine and Geevor Mine - Underground in Wheal Mexico
Connect with us, Like us and Follow us on Facebook!
PhotoFile Cornwall supports CoaST and Sustainable Tourism